We will discuss the key causes of pump impeller cavitation, and the best ways to prevent it.
Pump Impeller Cavitation In Depth
Pump impeller cavitation is the formation and subsequent collapse or implosion of vapor bubbles in a pump. It occurs when gas bubbles forn in the pump due to drop in absolute pressure of the liquid below vapor pressure.
These gas bubbles occupy space inside the pump and affect the pump’s operating pressure and flow. With vapor bubbles in the low-pressure zones of the pump, the motor’s energy is wasted expanding the bubbles instead of bringing more liquid into the pump. When the vapor bubbles collapse inside the pump, the liquid strikes the metal parts at the speed of sound. The noise generated from these collisions of gas bubbles into the metal parts of the pump, it sounds like attempting to pump marbles and stones.
Causes of Pump Impeller Cavitation
The difficult part about maintaining pump impeller cavitation, is that there is multiple reasons that can cause cavitation. There are many influencing factors that contribute to forming cavitation. The key causes of cavitation include the following:
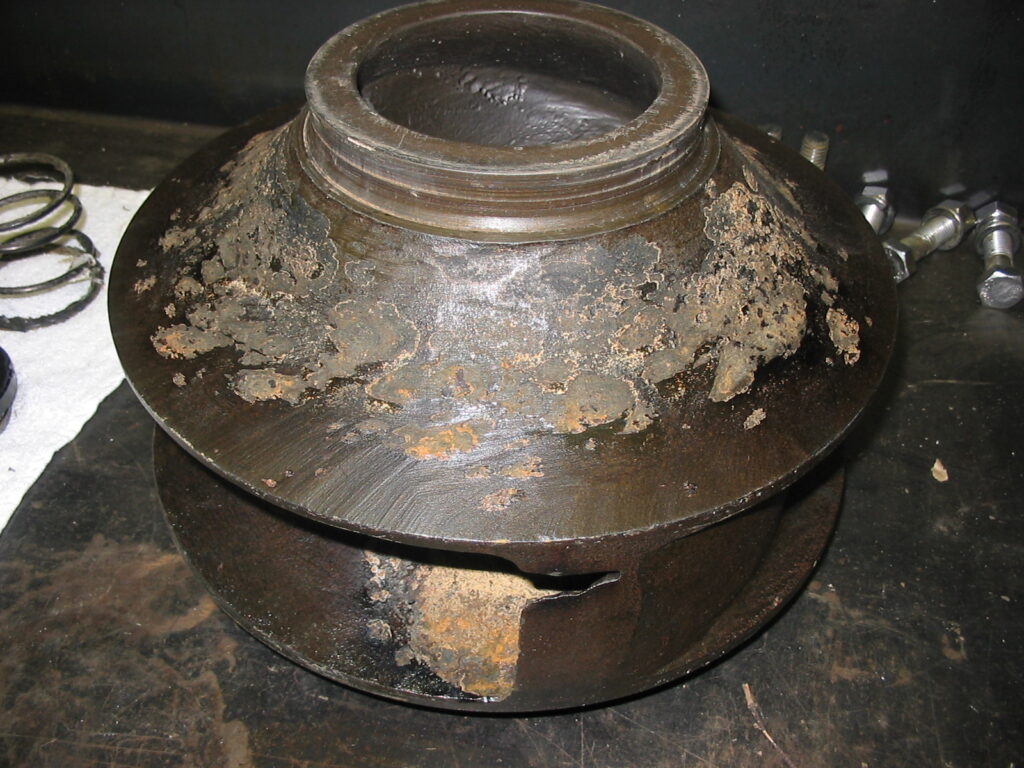
- Drops in pressure at the suction nozzle, if the fluid at pump suction is not available sufficiently above the vapor pressure of liquid at operating conditions, then vaporization of liquid and formation of gas bubbles is very likely, leading to cavitation.
- Increases in the temperature of the pumped liquid can increase the vapor pressure of the liquid. Thus, it becomes more likely for operating pressure to fall below this vapor pressure limit, hence leading to bubbles and pump impeller cavitation.
- Increase in the fluid velocity at pump suction can typically be caused by higher liquid flowrates than the design case. Frictional pressure drop in the pump suction also rises with rise in the flowrate, making low pressure and cavitation at pump suction more likely to occur.
- Undesirable flow conditions can be caused by obstructions in the suction piping such as sharp elbows, valves, other fittings and obstructions cause more frictional pressure loss in the pump suction, thus increasing possibility of low pump suction pressure leading to pump impeller cavitation.
Solutions and Prevention
Cavitation, as you can see, has many causes. But with many problems comes with many solutions. To prevent pump impeller cavitation due to vaporization, perform the following:
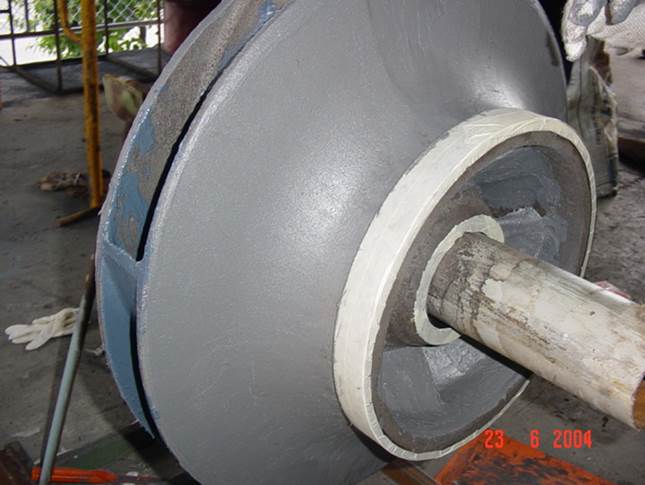
- Lowering the temperature of the pumped liquid.
- Raising the liquid level in the suction vessel.
- Changing the pump to a less corrosion prone materials.
- Reducing motor RPMs can in turn also prevent extremely high flowrates, a key cause to vaporization.
- Increasing the diameter of the impeller eye can add less space for liquid to boil or vaporize.
- Adding a pump/impeller inducer. Pump inducers prevent significant cavitation by adding a smoother inlet for pumped liquids or materials.
- Install two lower capacity pumps running in parallel to prevent large amounts of strain on a single pump.
- Use a booster pump to feed the principle pump. Booster pumps are machines that increase the pressure of a fluid, generally a liquid. It is similar to a gas compressor, but generally a simpler mechanism with only one stage of compression.
- Sealing the impeller/propeller with an epoxy solution, such as our own PES-201, can seal and protect the components from erosion and corrosion by adding a protective barrier between the devices and material it is pumping.
short article but straight to the point.
Good one!
Excellent article on Pump Impeller. Reading this gave me an idea of Impeller. Thanks for sharing your information.