Pumping systems account for 20 percent of the world’s electrical demand and the cost of energy represents 95 percent of the cost to run pumping equipment, so it is no surprise that all industry would benefit from any solutions aimed at increasing pump performance.
Several physical and mechanical problems can be suffered by fluid handling equipment, including general and/or localized corrosion, cavitation or reliability linked with poor efficiency or performance. All these parameters can affect the power consumption of the equipment, which increases its lifetime running cost considerably. A major consideration for pump manufacturers and uses is minimizing performance deterioration.
Other than corrosion resistant alloys, one way to effectively reduce the loss of equipment performance is to protect pumping systems using erosion/corrosion resistant epoxy coatings and in this area PES Solutions Metal Ceramic enhanced product range is based on the latest solvent free epoxy technology and is ideally suited to rebuilding and resurfacing equipment and components in a fluid flow environment.
Coating Effectiveness
The quality of the coating, preparation and application are critical to the life of any coating. The effectiveness of a coating depends on many factors:
- matching the coating to the intended service exposure
- the type of preparation for the coating
- the type of coating
- the type of corrosion involved
- the velocities the part will be exposed to
- the type of fluid
- the amount of abrasive particles
Our management team here at PES-Solutions has a combined 75 years of industrial experience of formulation and manufacture of cold applied coating for the protection of fluid handling equipment. Our Metal Ceramic enhanced product range offers a unique hydrophobic surface combined with high erosion/corrosion resistance, which reduces friction losses and thus the energy input required.
PES-Solutions Fluid Flow Protection
Any type of deterioration will greatly reduce the efficiency with which the pump is running. It is crucial to find solutions to reduce these effects and to extend the lifetime of equipment. Pump manufacturers have been looking at different ways to reduce corrosion and erosion damage onto metallic substrate.
The PES-Metal ceramic enhanced product range is based on the latest solvent free epoxy technology and is ideally suited to rebuilding and resurfacing equipment and components in a fluid flow environment.
The product range has been designed to be easy to apply, offer good chemical resistance and excellent impact and abrasion resistance in the most aggressive environments. Whether for sewage, salt water, aggressive chemicals or aggregate slurries our products are proven to perform within industry. The PES-Metal Fluid Flow Protection Range Has Been Used in the Marine, Power, Chemical, Oil and Gas, Water and Paper and Pulp industries.
Chemical Pump Impeller Before, During and After Our Metal Ceramic Products
Before:

Blasted:

Finished Result:
Pump impeller with Metal Loss from Cavitation
Cavitation Repaired PES Power Metal 201:

Impeller Coated with 1st Coat of PES Power Metal 203 Grey:
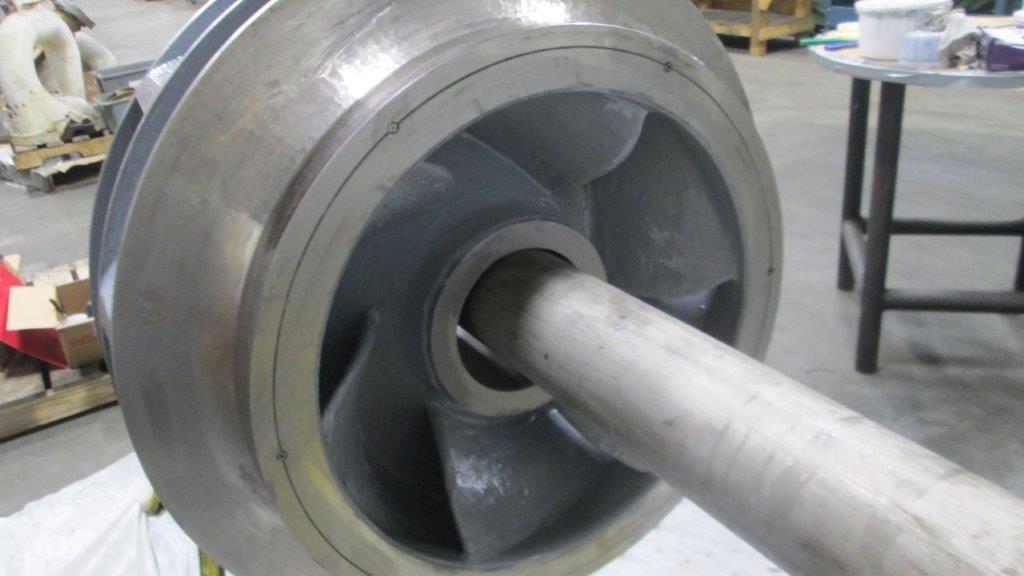
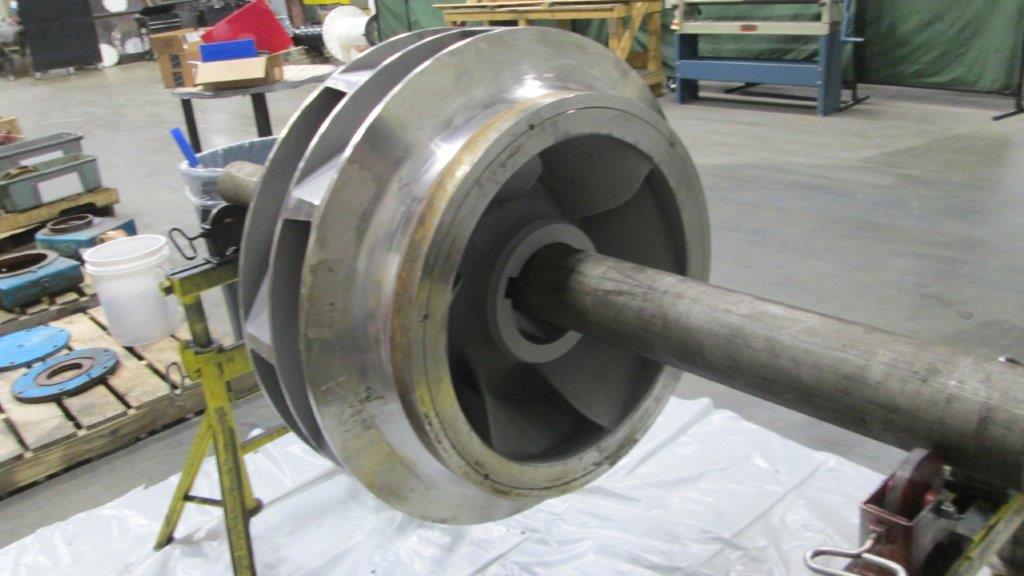
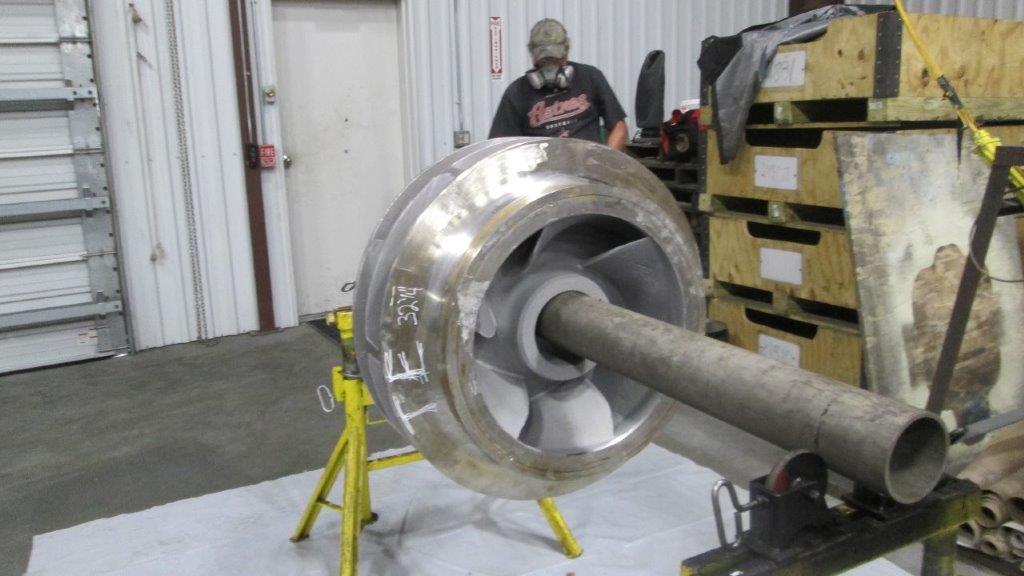
2nd Coat Blue:
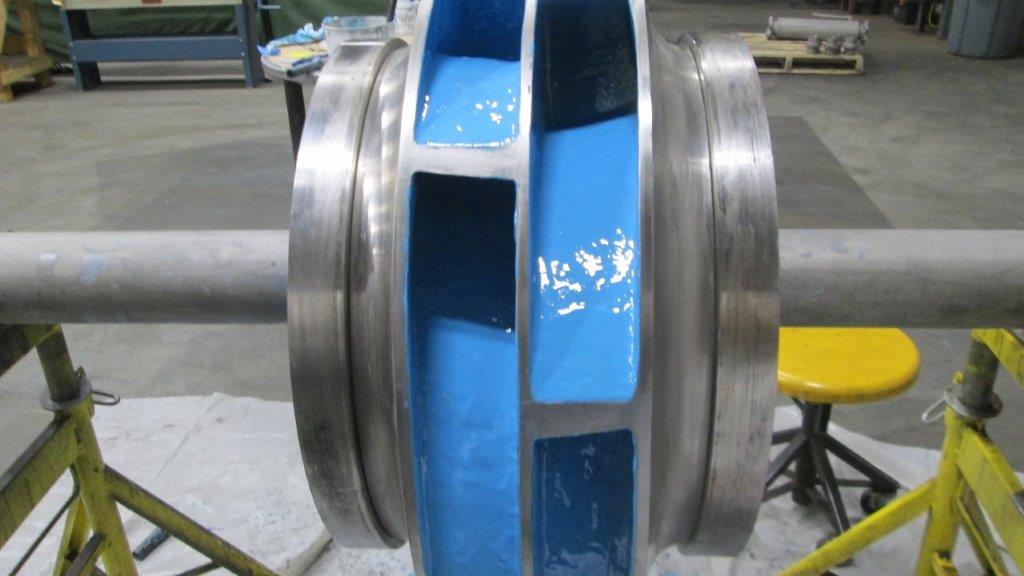
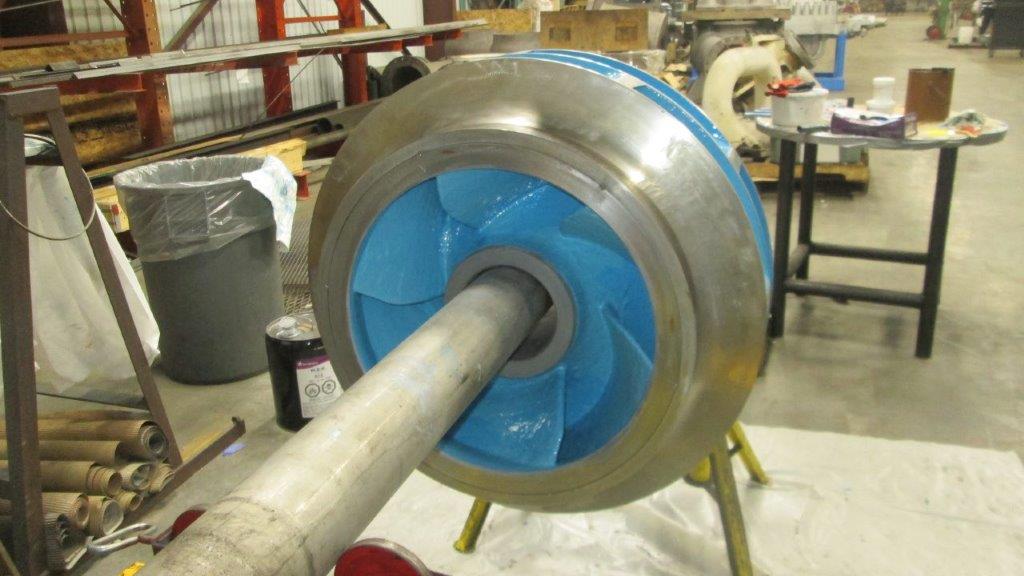
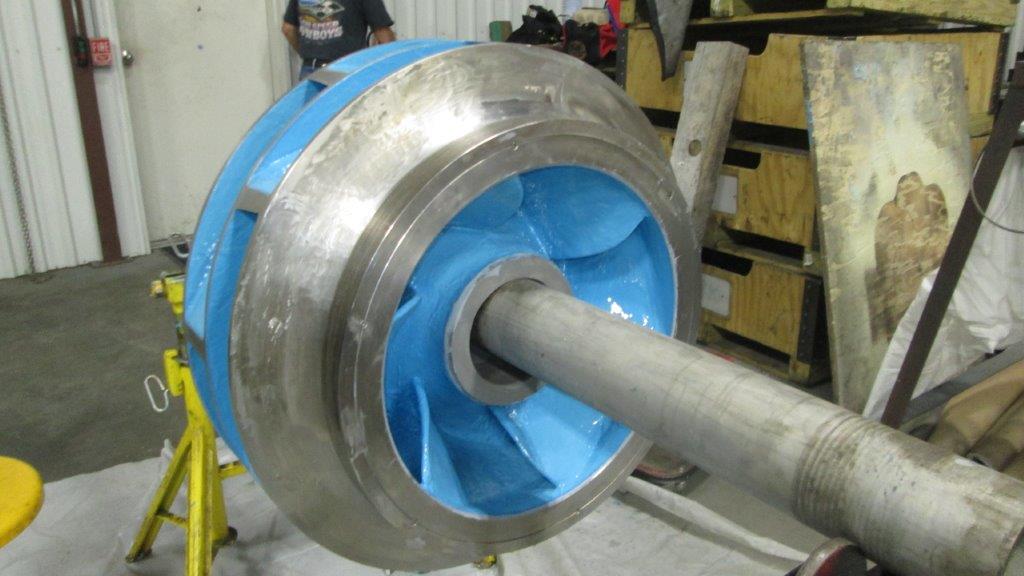
Plant Equipment & Services, Inc. is a regional sales and service company serving primarily the power industry in Texas, Oklahoma, and Louisiana. Our goal is to assemble and utilize our management teams’ vast experience and knowledge to solve any of your maintenance needs. Contact us with the link below for more information on how you can increase your pump performance with our PES-Metal Ceramic enhanced products!
sir,
We are considering ceramic coat for pump impeller and looking for detailed additional information on the subject to take final decision on ceramic coating of pump impellers and casing inside surface. We would like to know the ceramic material details and easy method to coat the parts. We would like to know the life of it , its advantages, its economical advantages, aND COST OF IT. iS IT ESTABLISHED PROCESS FRO PUMP PARTS.
Hello,
Yes, our ceramic coatings help increase pump performance, while at the same time decreasing erosion caused by abrasion, cavitation, and corrosion. Feel free to look at our 200 series ceramic filled repair compounds and coatings for further details.
PES 200 Series Ceramic Repair Data Sheets
If you have any further questions, give us a call at (979) 779-8700 or send an email to pes1@pes-solutions.com. We’d be happy to help answer any questions not covered in our data sheets.