Ceramics have been used by the power industry for years as a cost-effective, wear-resistant material. Ceramic material gives continuous protection to fan linings, chute liners, hopper bottoms, and dozens of other stationary high-wear points. Now, the technology
is available for using ceramics on moving parts as well.
In this article we will be using exhaust fan blades as an example!
The Advantages
In addition to the obvious advantage of longer wear life, ceramic wear bricks have several benefits that may not be immediately apparent:
- Lighter weight – Ceramic has only 40% the density of steel. A 1/8″ overlay of ceramic on a 5/16″ steel plate weighs 55% as much as a 3/8″ deck plate blade. This allows the use of an extended-length blade without creating undue stress on the spider. It also means that bearing life may be extended.
- Even wear – Unlike most hard-facings, ceramic is an extremely uniform material. There are no hard or soft spots that wear at uneven rates. This means that re-balancing of the fan between overhauls is almost eliminated.
- Minimum downtime – ceramic composite fan blades allow fans to run much longer by eliminating the major sources of unscheduled downtime.
Used Wherever Moving Parts Receive Abuse
Ceramic composite fan blades are now quite common in utility boilers where exhaust fans are used to blow pulverized coal into the boiler. Steel fan blades and whizzers that would last only two to three months have been replaced with ceramic composite fan blades that are still running after four years.
Industry-Proven Ceramic Wear
Provide Unmatched Performance ceramic composite fan blades have been successfully tested and proven in power plants around the world. Some fans are still in service after 35,000 hours of use.
Numerous Applications
In addition to power plants, ceramic wear bricks are common in manufacturing of:
- Cement
- Chipboard
- Asphalt
- Steel
- Numerous other manufacturing environments handling abrasive materials.
Design Advantages
- Structural Bonding – Provides opportunities for custom designs that are not available with hard-facing or coatings. The ceramic used is a fully-dense, fired body, not a porous flame-sprayed coating. By using small tiles rather than a continuous coating, the blade can flex and twist with no damage to the individual tiles.
- Strength and Versatility – Special shapes are used to protect the leading edge of the blade. The structure of the blade can’t erode out from under the ceramic. In high-wear areas, an extra layer of ceramic is inlaid to prolong the life of the blade. The tiles can be applied in special staggered patterns to prevent wear along the joints.
- Bolted-In-Place Applications – ceramic composite fan blades come with special bolts which have either a ceramic cap bonded to the top or a tight-fit cap bonded to the bolt top after installation. The choice of bolt caps depends on the wear pattern of the particular fan. If wear occurs over the bolt pattern, tight-fit caps are highly recommended. All the tools, materials, and instructions needed for cap installation are provided with each blade.
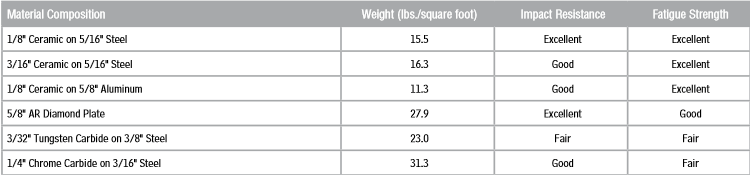
PES Solutions is the local expert on Ceramic Brick Wear, and they are more than happy to answer any questions you may have about their services.