PES-CHEM 501 CRSG is a high build solvent-free epoxy coating designed for the long-term protection of steel and concrete structures against corrosion and chemical attack.
PES-CHEM 501 CRSG
- Apply to mechanical, hydro-blasted or abrasive blasted cleaned surfaces
- Cures at temperatures as low as 41°F
- Apply to metallic surfaces suffering from condensation/dampness
- Ideal for protection against corrosion and low concentration chemical immersion
Typical Applications
Cold water lines | Pipework | Internal & external tank surfaces |
Structural steel | Sheet/bearing piles | Chemical intake areas |
Process equipment | Sumps | Chemical containment and bund areas |
Surface Preparation
Metallic Substrates – Abrasive blast cleaning
- All oil and grease must be removed from the surface using an appropriate cleaner such as MEK.
- All surfaces must be abrasive blasted to SSPC/ NACE 2 (ISO 8501/4 Standard SA2.5) minimum blast profile of 3 mils using an angular abrasive.
- Once blast cleaned, the surface must be degreased and cleaned using MEK or similar type material.
- All surfaces must be coated before gingering or oxidation occurs.
PLEASE NOTE: For salt contaminated surfaces the substrate must be pressure washed with clean water and checked for salt contamination, please refer to the surface preparation and pre-application guide for further information.
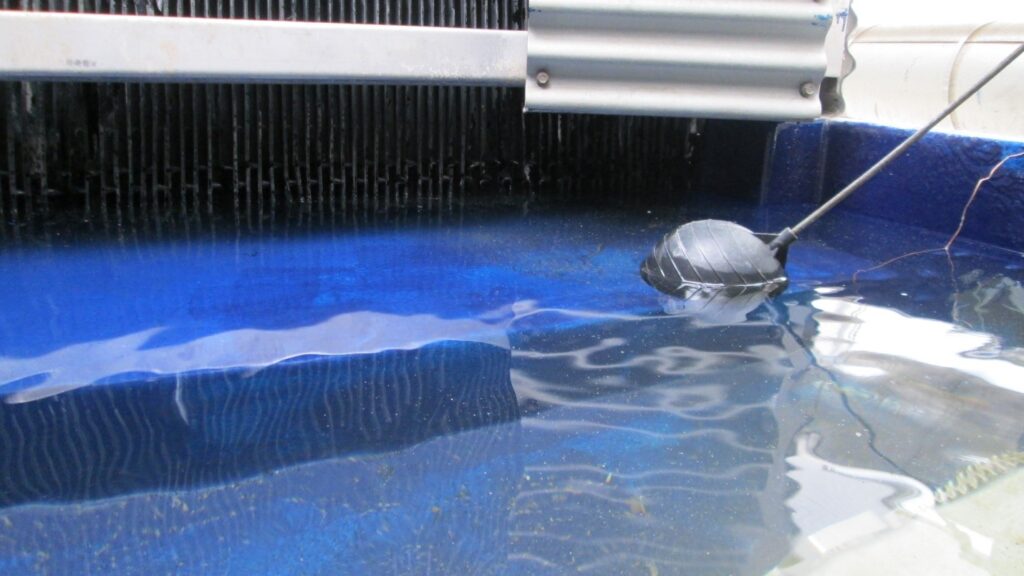
Existing Concrete
- If the concrete surface is contaminated, pressure wash using clean water.
- Once the concrete is dry, lightly abrasive blast or scarify taking care not to expose the aggregate.
- Clean all dust and debris from the surface and prime with PES-CHEM 503 SPEP (low viscosity epoxy primer).
- Apply PES-CHEM 503 SPEP at 6mils WFT, leave to cure for 3 hours (68°F) before overcoating.
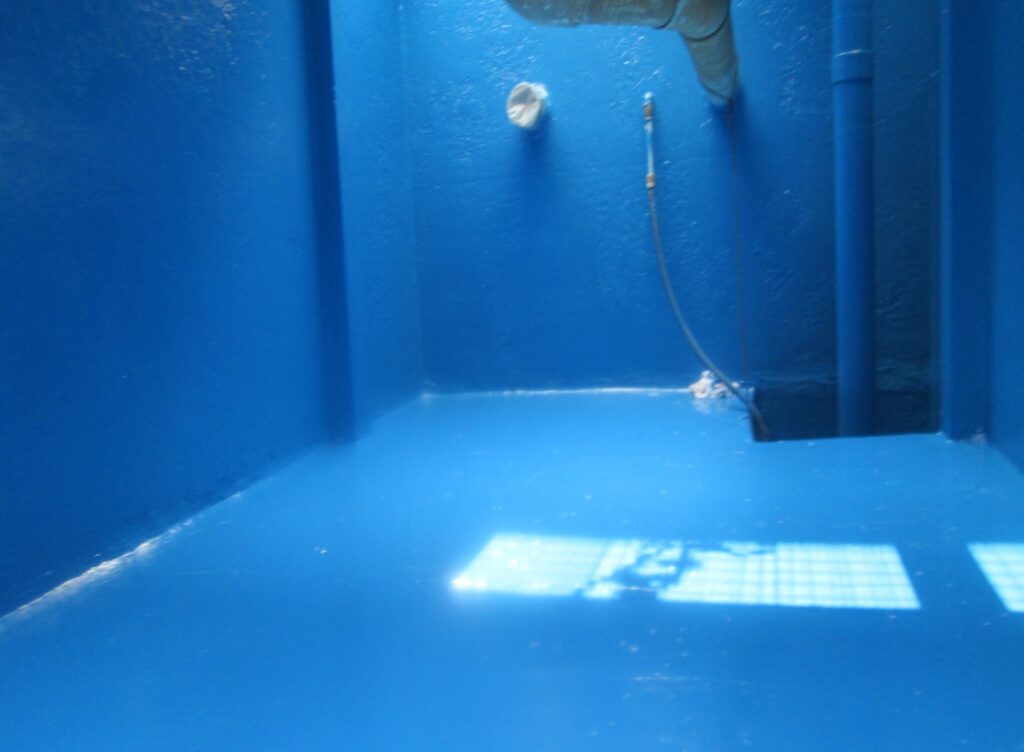
Application
Brush or roller applications:
- Pour the mixed material into a paint kettle or paint tray (this will maximize the usable life).
- Using a 2″ wide synthetic brush, stripe coat all edges, joints, corners and equipment with the mixed material. The stripe coat must be approximately 4″ wide, at 10mils wet film thickness.
- Once the stripe coat has cured sufficiently and is capable of being overcoated, apply the 1st coat of mixed product to all surfaces at 10mils wet film thickness.
- Once the 1st coat of material has cured sufficiently, approximately 4 hours at 68°F, apply a 2nd coat of material to all surfaces at 10mils wet film thickness.
Coverage Rates
0.8 gal (3.4ltrs) of fully mixed product will give the following coverage rates –
146ft2 at 10 mil – 13.6m2 at 250 microns
4.2 gal (16ltrs) of fully mixed product will give the following coverage rates –
688ft2 at 10 mil – 64m2 at 250 microns
Please note that the coverage rates quoted are theoretical and do not take into consideration the profile or condition of the surface being repaired.
Cure Times
At 68°F the applied materials should be allowed to harden for the times indicated below before being subjected to the conditions indicated. These times will be extended at lower temperatures and reduced at higher temperatures:
Usable life | 30 minutes |
Minimum overcoating time | 4 hours |
Maximum overcoating time | 36 hours |
Water/sea water immersion | 3 days |
Chemical immersion | 5 days |
Pack Sizes
This product is available in the following pack sizes –
0.8 gallons (3.4ltr), 4.2 gallons (16ltr).
Color
Base component – Light Grey, Dark Grey, Red or Blue
Activator component – Amber
Over-coating times
Minimum – the material can be over-coated as soon as it is touch dry, approximately 4 hours at 68°F.
Maximum – the over-coating time should not exceed 36 hours.
Where the maximum over-coating time is exceeded, the material should be allowed to harden before being abraded or flash blasted to remove surface contamination.
Storage Life
5 years if unopened and store in normal dry conditions (60-86°F)
Other Technical Documents
Safety Data Sheets – Base & Activator components
Product Specification Sheet – Technical Performance Information
Health and Safety
Please ensure good practice is observed at all times. Protective gloves, goggles & a disposable coverall must be worn during the mixing and application of this product. Before mixing and applying the material, ensure you have read the fully detailed Safety Data Sheet.
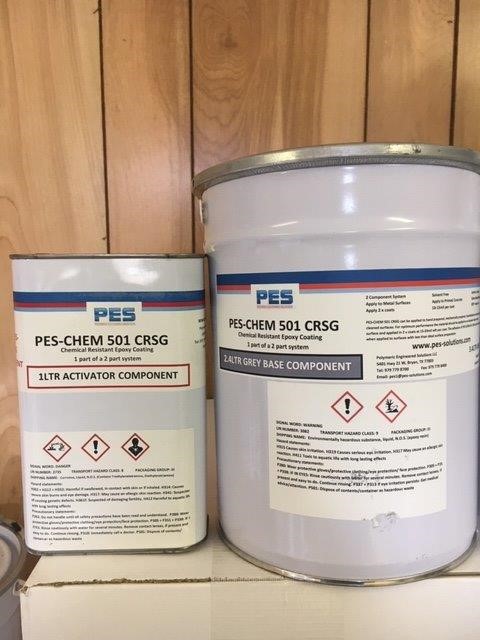