With years of experience providing Polymeric Engineered Solutions, our team is committed to resolving deterioration and corrosion using our PES products. The following are just a few of the many solutions our PES products have provided.
Success Stories Using PES Products
Tube & Shell Heat Exchangers & Chillers
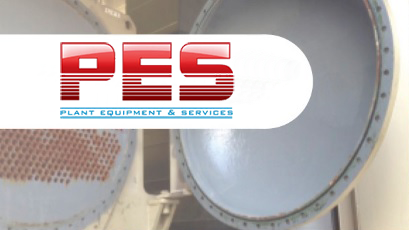
The Problem: The surfaces of a heat exchanger had become worn and pitted through corrosion. The exchanger required rebuilding and coating to protect against future damage.
The Solution: To rebuild the steel substrate with PES 201 Ceramic Repair Paste and PES 202 Brushable Ceramic Repair Fluid, & PES 203 Superflow Ceramic Fluid.
The Application: The steel substrate was abrasive blast cleaned to SSPC SP10/NACE 2 Near white Metal, W/ 3-4 mil angular anchor pattern,( SA2.5 with a 75 micron profile, ISO 8501/4 Standard SA2.5).
The exchanger tubes were filled with cork and surface leveled with application of PES 201 Ceramic Repair Paste. The exchanger tubes then had two coats of PES 202 Ceramic Repair Fluid, & 1 coat 203 Superflow Ceramic Fluid applied to a nominal 10-12 mil per coat.
Tank External
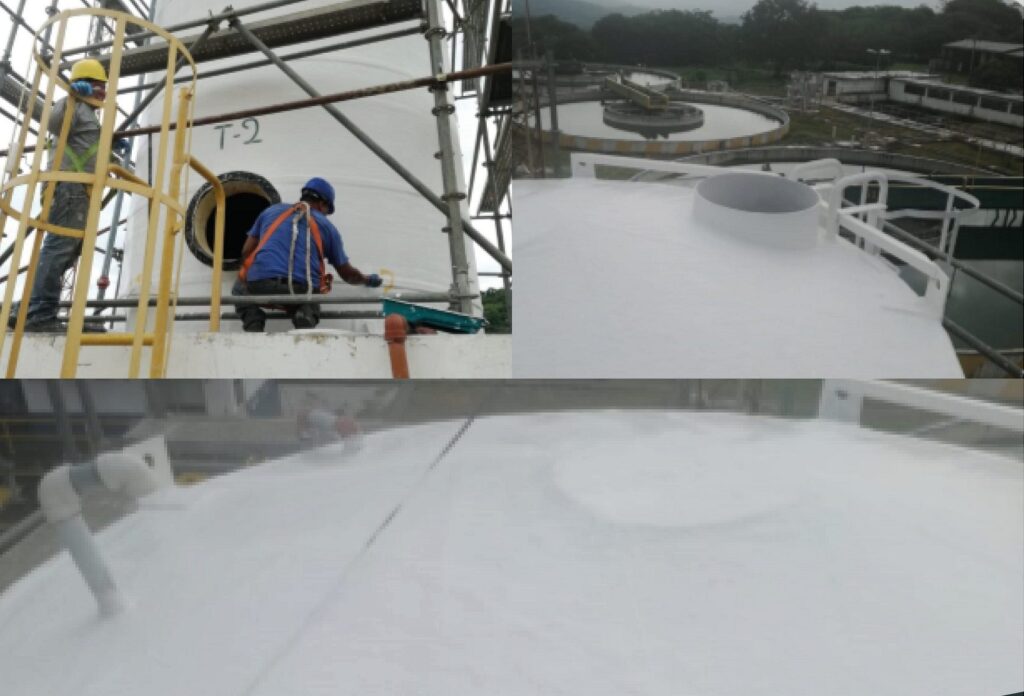
The Problem: Industrial site with aged storage tanks required a long term UV stable coating. This coating was to protect assets against any future deterioration. A system requiring minimal surface preparation was necessary to reduce the application time frame.
The Solution: Pressure wash the existing coating to prepare the surface.
The Application: Existing coating pressure washed to remove loose material and other contaminants.
2 coats of PES-CHEM 555 applied by brush, roller and where possible by airless spray to a total nominal dry film thickness of 20 Mil each coat.
Pipe Field Joint Coating
The Problem: Polypropylene coated pipeline required coating for the exposed steel work around field joints.
The Solution: Prime surface with PES 530 HA100 and over-coat with flame sprayed Polypropylene.
The Application: Steel substrate abrasive grit blasted to SSPC SP10 /NACE 2,W/ 3-4 mil angular anchor pattern (SA2.4 with a 75 micron profile, ISO 8501/4 Standard SA2.5).
A 2″ band of polypropylene on each side of the joint are abraded with mechanical hand tools to create a rough finish.
PES 530 HA100 heated to 122° f and applied the joint area at 12-14 mil. by brush. Polypropylene flake then flame sprayed into the surface. A final flake treated application of polypropylene was applied to the joint to create a seamless finish around the entire length of the pipe.
Swimming Pool Overflow Tank
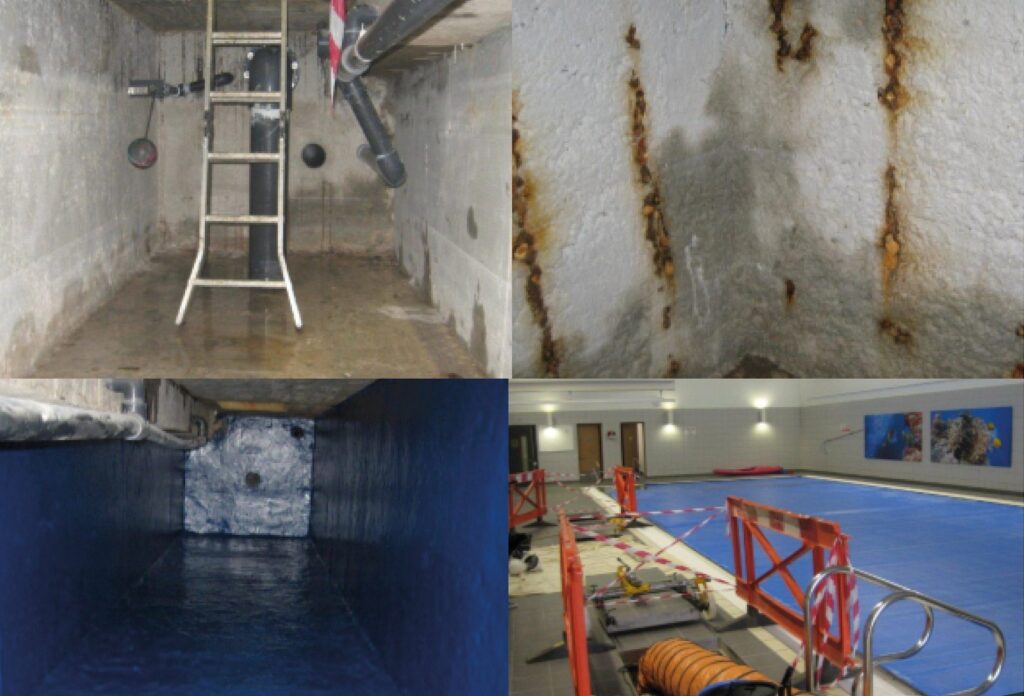
The Problem: Concrete overflow tank leaking water due to degradation of the substrate.
The Solution: Repair damaged concrete and coat tank with PES 507 DWPU.
The Application: Top layer of concrete removed by blasting and grinding.
Damaged sections repaired using 574 Grout.
All surfaces primed with PES 503 SPEP. Then, the surfaces were over-coated with 2 coats of PES 507 DWPU, applied by brush and roller at 14-16 mil per coat.
Salt Water Pump
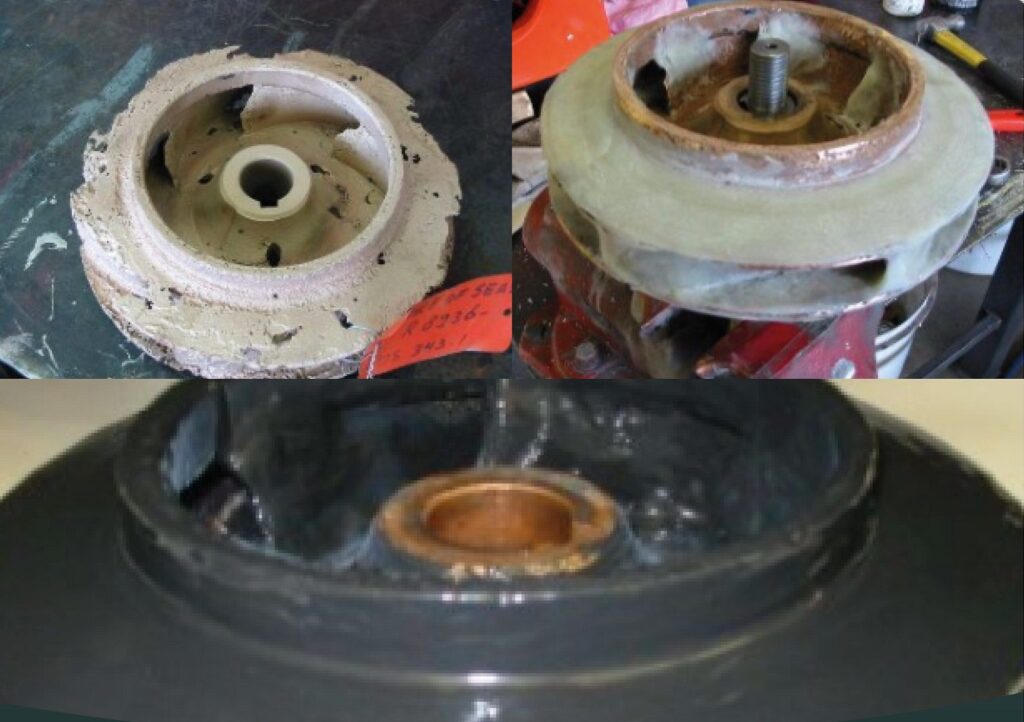
The Problem: Salt water pump heavily worn through abrasive required rebuilding and coating with an abrasion resistant finish.
The Solution: Rebuild lost steel with PES 101 Power Metal Paste. Protect with PES 202 Ceramic Repair Fluid.
The Application: Steel substrate abrasive blast cleaned to SSPC SP 10 /NACE 2 w/ 3-4 mil angular anchor pattern, (SA2.5 with a 75 micron profile, ISO 850/4 Standard SA2.5).
In order to fill and rebuild the damaged sections, pieces of PES 1064 flexible tape were cut to create a matrix for the 101 Power Metal Paste to build around.
Once cured the PES 101 Power Metal Paste was machined smooth and then over-coated by brush with 2 coats of PES 202 Ceramic Repair Fluid at a nominal 12-14 mil per coat. Always check impellers to see that they are balanced after making repairs.
Our team at PES customizes solutions and repair services depending on the severity and the type of problem. Contact us with the link below for more information or to get a quote on your repair project today!