It’s time to tune up and maintain your HVAC equipment
Chillers are one of the most important pieces of equipment for your heating and cooling needs. Along with all the mechanical repairs and upgrades, be sure to complete a corrosion / erosion upgrade to your Tube Sheets and assorted wet attachments, such as Water Boxes and End Bells. Plant Equipment & Services Corrosion and Erosion Repair and Maintenance system will get your chiller into top operating performance.
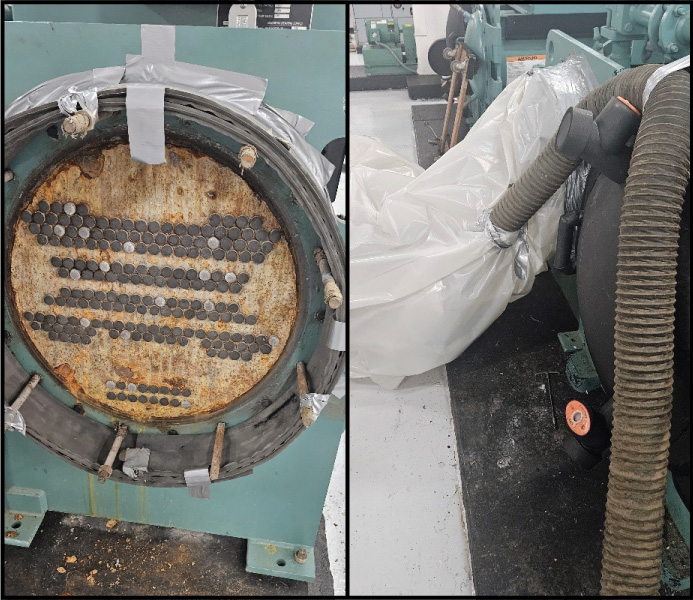
The first step to our system consists of building dust containment barriers and installing blast plugs to protect inside areas of chiller tubes before abrasive blasting. Next a thorough cleaning of the Tube Sheets and assorted equipment to a NACE #2 level SSPC SP10 Near White Metal is performed, then wipe down all freshly cleaned surfaces using a clean-dry solvent such as MEK or Denatured Alcohol. This will remove any oils, grease, or dust from areas to be repaired and coated. The Tube Sheets are then coated and built up with the end of the tubes with our PES 201 Ceramic Repair Paste Grade compound to aid in a long-term erosion barrier on the Tube Sheet area caused by turbulence from the high volume of cooling tower water, and to add protection from bimetallic corrosion (when one metal, such as carbon steel tube sheets, corrodes to protect the copper alloy tubes).
PES 201 Ceramic Repair Paste applied around the tubes flush with the end of tubes
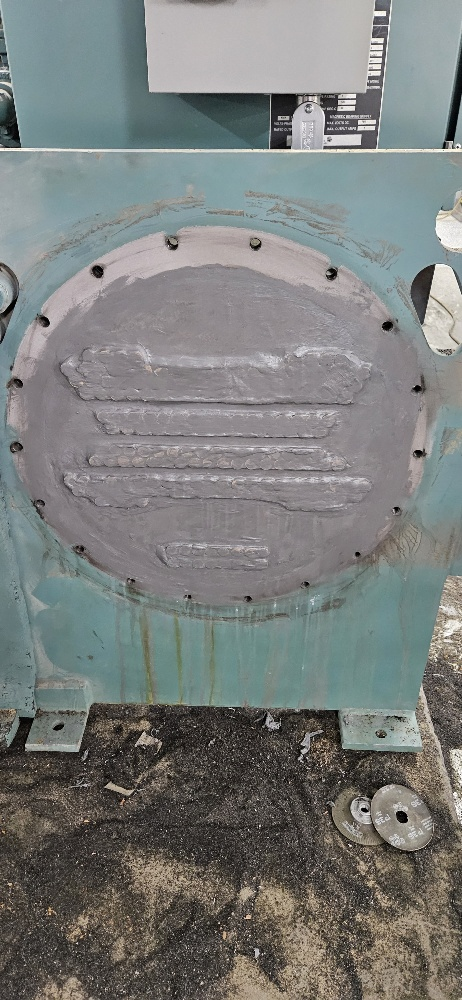
The next procedure in the step-by-step corrosion protection system is to apply 2 coats of two different colors of PES 202 Ceramic Repair Fluid and a final coat of PES 203 Super Flow Ceramic Fluid. Your chillers are receiving 45–60 mils plus in corrosion protection, where some companies only recommend 15-20 mils, giving years less in protection.
After finished coatings have had time to reach a light load cure, usually overnight, Tube Sheet and assorted parts are low-voltage sponge tested for holidays or pin holes in coating and marked for repair if needed.
Coating plugs (corks) are then tapped in the tube slightly, then using a 3/8” drill with a carbide honing stone, the tube entrance is slightly ground creating a slight bevel (chamfer). This chamfer aids in tube brushing and eddy current testing. Corks are removed, and a final visual inspection is performed. If any touchups are needed, they will happen at this time.
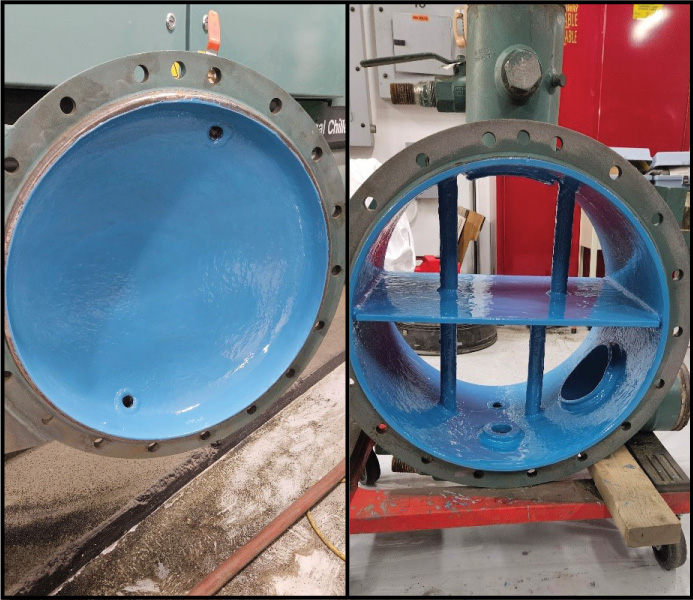
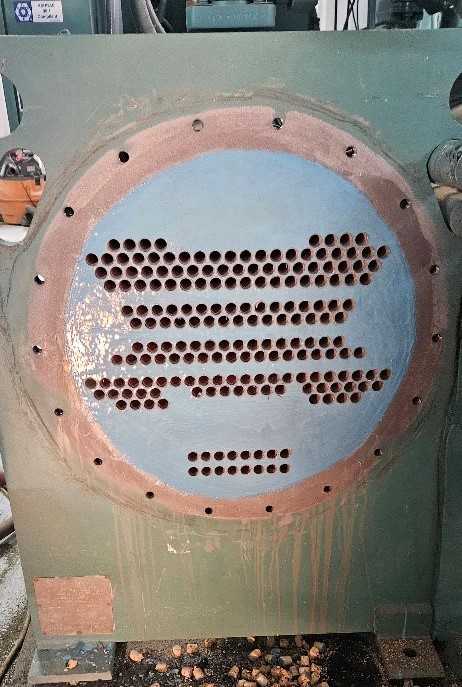
After the final cleanup, the chiller is put back into service with many years of corrosion protection ahead of it. When purchasing PES products, we will train your maintenance personnel or your contractor. If you prefer, PES can provide a turnkey service for this application. Please contact us at pes1@pes-solutions.com or call 979-779-8700 for more information and a quotation.